Production
Project & design
Thanks to its facilities and highly skilled staff, Salentec is able support the customer in each step of the product developement, from the mechanical and functional project of the device, to the aesthetic design, by means of:
- 3D CAD editing, modelling and FEA analysis;
- CNC or 3D priting of prototypes and first series;
- Development on customer request;
- 3D Optical measurement (GOM technology) for relief and certification of dimensional data and/or to make reverse engineering;
- Mechanical properties analysis (strength, stifness, toughness, fatigue, microstructure, …);
- Luer compliance verification according with standard requirements (ISO 80369-7:2016, ISO 80369-20:2015, …)
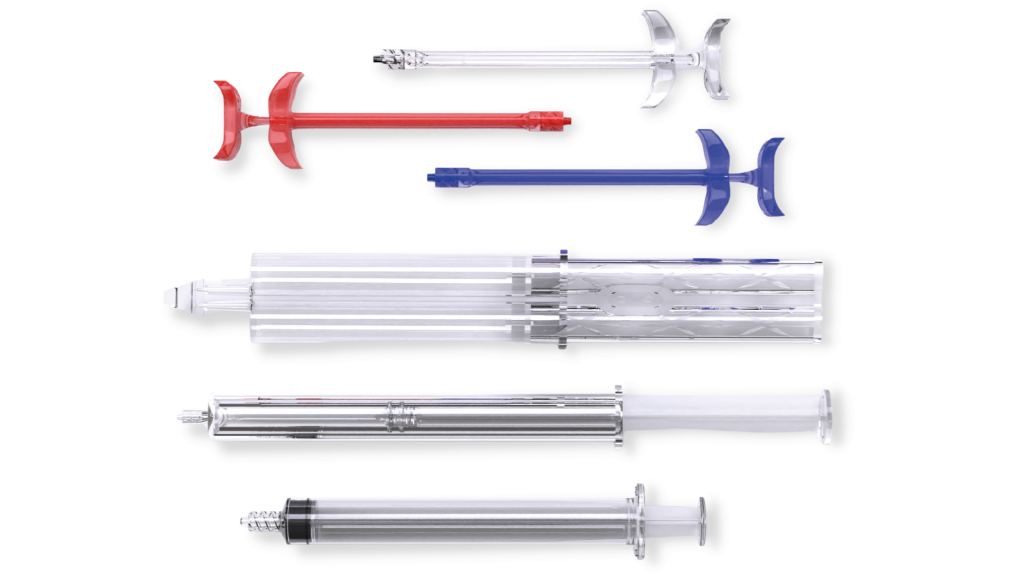
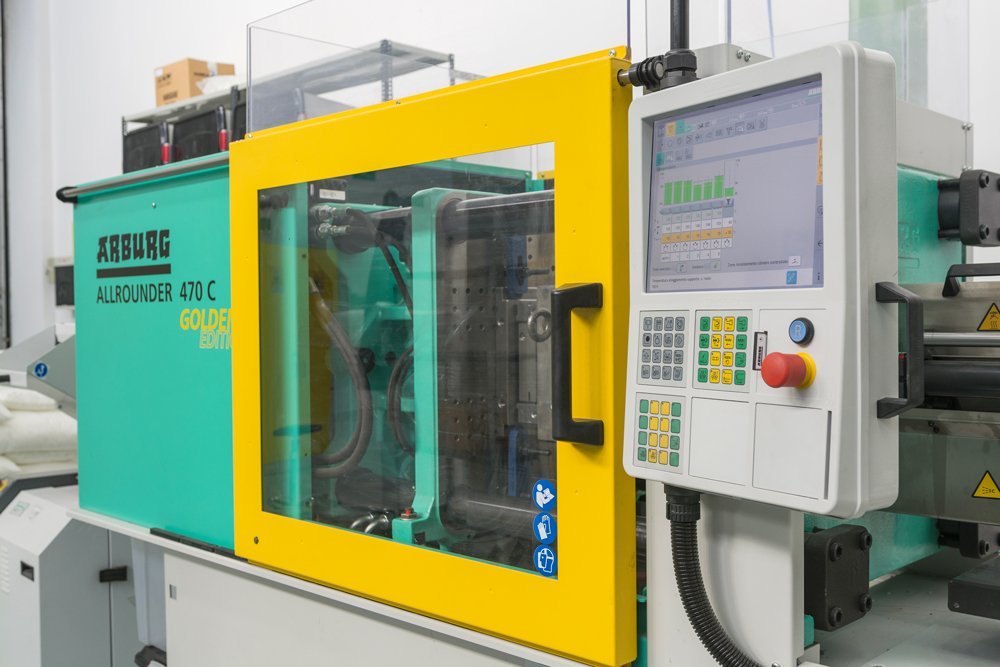
Injection molding
All the syringe components are injection molded with the best injectors availble on the market.
The automized production lines are designed to ensure the maximum flexibility for the introductionof new models, allowing the realization of customized supplies, from few thousands to milions of part per year.
The demoulding and manipulation of parts is fully automized and integrated with a vision system, that operates a first level check on the 100% of products.
Materials
The components can be realized with all the thermoplastic admitted in the specific field and proposed by our customers.
The base material used by Salentec for the barrel production is a cyclic olefin copolymer (COC) – TOPAS 6013 – a techno-polymer compliant with EP, JP and USP class VI (DMF12132).
According the specific functional and aesthetic requirement of our customer, we can manufacture parts in COC or COP, PETG, PA, PP, PC, strictly in medical grade, for the accessories production (plunger, finger grip, etc). It is possible to customize colours and geometries, to apply logos or friezes.
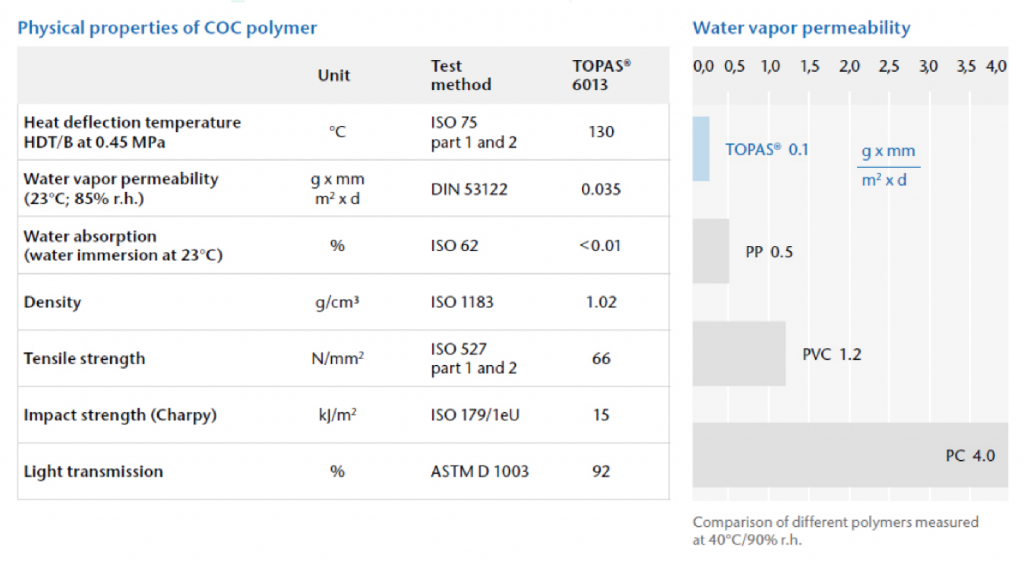
The main characteristics of COC:
Excellent humidity and vapour barrier
Transparency (easthetic effect similar to glass)
No release of ions or metals
Non polar surface of syringe
Quality checks - Siliconing - Packaging
Products are controlled and packed in classified environment (ISO 7 clean room).
Each barrel undergoes a second level optical check by means of optical systems up to 4x; the products are subsequently washed and dried.
The siliconing step is fully automized; flow and quantity of sprayed silicone are continuously checked and measured, in accordance with the standard reference.
The products are finally packed and sterilyzed; before the sale, severe checks are performed on the contamination level, bioburden, heavy metals, silicone quantity.